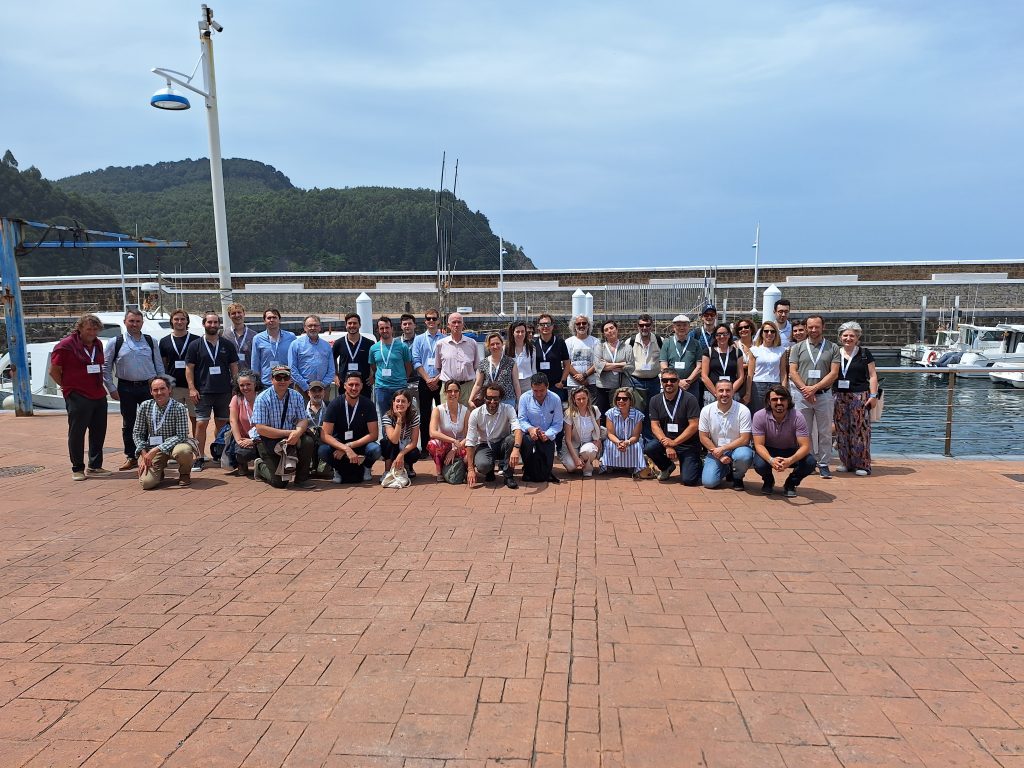
News
News
8 November 2017
The induction system is currently in the testing phase at our facilities in Irun and two new prototypes for steel and iron are under construction
The metal transforming industries, like foundries, require an important energy supply for their processes, particularly electricity. At TECNALIA, we have developed a system for wireless smelting furnaces which transmits energy through air via an inductive coupling system, whose objective, among others, is to save more than 25% of the energy involved in the entire part casting process and hence improve the service and the competitiveness of companies, whilst reducing environmental impact and costs. The system is currently in the testing phase at the facilities of TECNALIA's foundry pilot plant in Irun, a semi-industrial prototype that is capable of casting 180 kg of steel or iron (process temperatures of 1,600 ºC or 1,450 ºC respectively) with a transmitted power of 100 kW. This solution is designed by and for the European smelting sector and focuses on three alloys that together amount to more than 90% of the metal smelted at foundries worldwide (iron, steel and aluminium).
The wireless connection system is designed to make the processes as flexible as possible, easily allowing distribution adjustments in complex plants with a high degree of variability in their workloads. In the current scenario, companies are increasingly demanding shorter response times, smaller series or batches and a high variability of parts. This complicates the production organisation at the foundries, making them energy-inefficient, especially when dealing with energy intensive consumers, and generating molten metal waste. This may lead them to lose orders due to the timeframe and/or for being inefficient in internal costs. The system enables the processes to be simplified with this new technology, leading to cost savings in production.
All of this is within the framework of the NIWE (New Induction Wireless Manufacturing Efficient Process for Energy Intensive Industries) European project, backed by the FP7 programme, which is led by Tecnalia and made up of a consortium of ten companies from Italy, Bulgaria and Spain, namely: Inductotherm-Ondarlan, Sematec, Krown, TECNALIA, Circe, Fonderie 2A, Foundries Association of the Basque Country and Navarre, Bilbobul, Furesa and Deguisa.